DMP was the result of a year-long investigation into the process of moulding Plywood.
I was fascinated by the fact that a process that produced a material that was so impressive in both its mechanical properties and efficiency had seen so little improvement in recent years. After I had gained an understanding of moulding plywood throughout the Kolmio manufacturing process, I set about trying to see if I could find a way of further evolving the process.
Something that immediately became apparent in my earlier experiments was that while the forming of plywood could actually be remarkably quick and simple, nothing could happen without a former. The production of these formers, especially when exact profiles or complicated geometries were required, could often be a very technically demanding task - far more difficult then simplify producing the moulded pieces. This effort was sometimes offset by the ability to reuse the mould multiple times, but in a low volume run the demand of producing a mould often outweighed the benefits of using moulded plywood.
What if the process could somehow be changed to negate the need for a former?
One of the first attempts at forming plywood without the use of a mould
It was discovered that to create accurate profiles, alignment was required throughout the entire piece that was being molded - which is why the 'spines' are necessary
Early experiments showed that successful moulds could be made without a former. However, whilst successful lamination without a former was progress, the process would be useless without the ability to accurately form pressings into the desired profile. After a lot of prototyping and experimenting, I discovered a method whereby I could pre-machine the plies, clamp them at a few select points, and produce accurate pressings without the need for a former.
A more developed prototype using both a central spine and plies that had been created using CNC machining
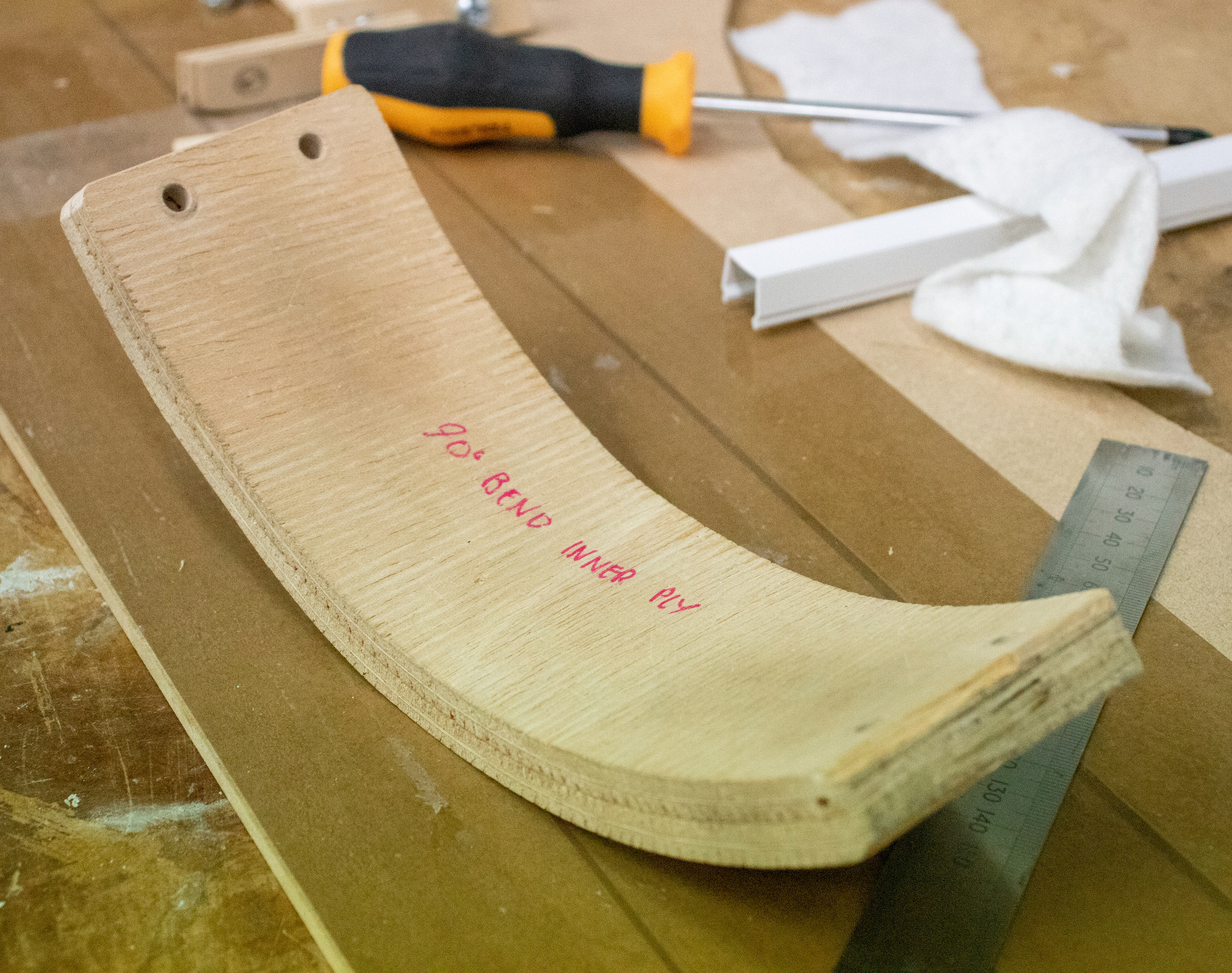
The pressing that proved the process could be technically viable
After establishing the Proof Of Concept, the challenge became how to optimise the process with a manufacturing environment in mind. Previous tests required extensive CNC machining - which took both a long time to complete and a long time to generate the required toolpaths. Whilst the toolpath generation would later be solved by the employment of algorithmic design software, it took a lot more prototyping to establish the most efficient way to machine the plies - reducing the number of tool changes, the number of plies requiring machining, and the overall time spent on the CNC bed.